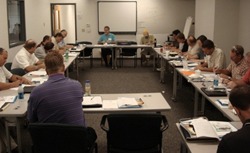
Going to the gemba — where the work is done — takes on new meaning for participants in AME Consortium activities. Leadership’s direct involvement in daily improvements signals keen interest and support, spurring employee engagement. And when they’re visiting other consortium members’ facilities — learning about effective ways to nurture day-to-day performance improvements — these lessons can help to ramp up lean progress, according to Kevin Shaver, vice president of operations at Velocity Machine Inc. in Green Bay, WI. With sales at $14 million, the company provides precision machining, fabricating, mechanical assembly and packaging solutions to OEM customers worldwide.
An example of shared learning, thanks to visits with fellow members of the AME Consortium Northeast Wisconsin Region: Velocity Machine adapted a system of color-coded visual tools signaling “hot” products versus those put on hold, after visiting another member’s facility. Now production employees record hour-by-hour updates on target rates compared to what is actually running, along with a note on any constraints such as inaccurate estimates. “This information offers a tremendous opportunity for potential improvements in different operations,” Shaver said. His standard work includes plant floor visits several times a day. “This shows that I care about employees taking the time to fill out the forms and work on improvements,” he added. He credited this new approach, built on employees’ suggestions, with double-digit efficiency improvements in a few months’ time.
The consortium provides the opportunity to meet, see and discuss common challenges with other manufacturing leaders, Shaver said. “My staff has been able to go to other facilities to see their processes and meet peers they can learn from, as well,” he said. “As a result, we have had smaller groups come back to our facility and we have been to other facilities to make a deeper dive into concepts that we can share and learn from. We have implemented processes and tools we have seen at other members’ facilities — with great success — and they, in turn, have learned from us.” Facility tours and speaker events open doors for benchmarking and new understanding. “We’ve heard from experts in various fields and gained training at reduced cost [sharing costs with other consortium members], allowing us to see and hear from experts who might not be available otherwise,” Shaver said.
Weighing In on Non-Manufacturing “Lessons Learned”
Learning from non-manufacturing consortium members is another plus. “We have the YMCA and other non-manufacturing organizations in the consortium,” Shaver said. “Everyone has a front end and a back end to their product where value stream mapping and other tools can apply.” He recounted that Velocity Machine launched a health committee, thanks to suggestions from YMCA representatives. Shaver projected potential insurance cost reductions as related programs take hold. Last year, Velocity sponsored a “biggest loser” weight loss program. After learning that some employees were reluctant to reveal their weight to others, the company plans to modify the program this year. Teams of four people will participate and will weigh in together on the shipping scale; no individual weights will be taken, so people are not intimidated by being weighed in front of others.
Networking
Personal connections through the consortium offer significant value, Shaver said. “There have been multiple times when I contacted a peer in our group and they have contacted me,” he said. “It could be to get more information on something we saw or discussed in one of our meetings, or about contact information for professional support or equipment. You get the opportunity to avoid making mistakes that someone else has already experienced and resolved. It can save you time, pain and money.”
Editor’s note: To learn more about AME Consortia and how you can share, learn, coach and improve with fellow lean/continuous improvement practitioners in your area, visit ameconsortia.org.
Lea Tonkin, president of Lea Tonkin Communications in Woodstock, IL, is the former editor in chief of Target magazine and Target Online.