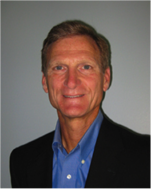
The school year has started and it is so gratifying to see the extent to which the student enrollment in my lean courses at Oakland University has grown over the past five years. In Fall 2008, we started with one lean course and 11 students; now we have two lean courses that maxed out with 45 students this term. OU students are getting into lean!
I could not teach these courses without special partnerships with some excellent lean organizations. This term, eight organizations and their leadership teams have opened their doors and cleared their calendars to work with our student teams. Several of them are first class lean manufacturers, such as Faurecia, Lear and Fitzpatrick Manufacturing.
More importantly, I could not teach these lean courses without the outstanding working relationship I have with these organizations. Not only do they conduct site visits for the students, give guest lectures and sponsor student team projects, they also participate in lean workshops that I hold during the summer months.
The lean workshops are my classroom where I continue to learn how lean really works on the factory floor and in the administrative offices!
This past summer, I led a lean workshop sponsored by a small manufacturing firm. The workshop was held onsite and consisted of six sessions (one per week) that lasted two hours each. The class was made up of 12 of the firm’s front-line employees, and attendance was perfect and punctual — better than my undergraduate students.
The employees were divided into three kaizen teams and each conducted a lean workout using the A3 Report methodology. See the lean workout A3 template I use below:
The key learning that I took away from this summer’s lean workshop is just how critical two lean tools, in particular, can be to the success of the lean workouts and an organization’s lean journey.
These two tools are not what most lean practitioners think of first, but they are mainstays of Toyota’s success. They foster employee knowledge, skills and attitudes that are essential to a successful lean transformation.
The two lean tools I’m talking about are: 1. an employee profit-sharing plan and 2. an employee suggestion program. The manufacturing firm was using one lean tool, but not the other, and the impacts were evident throughout the lean workout.
The firm had a longstanding employee profit-sharing plan that all employees participated in. Because of this, the employees were very aware of the current health of the business and the operational factors that affected their payouts. So when I talked about the changing competitive conditions, they knew what I was talking about and were all ears.
I had a rapt audience when it came to discussing shrinking lead times, higher quality requirements and necessary cost reductions in the new competitive marketplace. Why? Because all these factors influenced their money!
Every month, the employees tracked the plan payout in anticipation of a big year-end bonus. They knew what was happening in a general sense about customer orders, revenues and expenses. So when management and the three kaizen teams got together in the first session of the lean workshop to discuss potential problems to work on, the teams were anxious to look at problems with the tools purchasing and tracking process, out-of-control supplies spending and first-part quality inspections because they could see the impact on their money.
The kaizen teams immediately understood and implicitly answered the WIIFM question. They knew that if they could improve the tool inventory process and speed up first-part quality inspections they could reduce costs, improve lead times and make more money. That helped a great deal in increasing their engagement in the lean workout process.
On the other hand, what also was evident was the absence of an employee suggestion program. Not that the manufacturing firm hadn’t tried several times in the past to institute one. But, each time it did, very few participated and when the employees did participate, they often complained about toilet paper and other non-operational items. Management thought the employees were blowing it off and they didn’t respond, so the program went dormant for the past couple years.
Unfortunately, what was lost during that time was invaluable. Management lost the opportunity to learn how to listen and respond to employee ideas and concerns. More importantly, management lost the opportunity to gain the trust of the employees that it would listen to their ideas with respect and an open mind — even toilet paper ideas.
It was obvious in the lean workshop that the employees were doubtful that management would listen with an open mind to their recommended countermeasure and ideas about their target conditions. Management, as well, was skeptical that the kaizen teams would understand that capital wasn’t free and not propose big dollar countermeasures to fix the problems.
In other words, they hadn’t built the fundamental trust among themselves that comes with daily employee suggestions, frequent dialogues with management about new ideas and whether the ideas will work and/or be feasible under the circumstances. This kind of trust doesn’t just happen overnight.
Employee suggestion programs develop necessary skills and attitudes that many take for granted and don’t appreciate their value to the lean journey.
From an employee perspective, it is a learned skill to see a problem, diagnose a countermeasure, evaluate its effectiveness and feasibility and then express it in writing to supervisors and managers. Employees also need a built-up confidence that gets them out of their comfort zones so they “raise their hands” and suggest an idea that they think improves what everybody is currently doing. Not an easy action for many employees on the floor, or students for that matter, to do.
From a management perspective, it is also a learned skill to listen to employee ideas — good or bad, small or big — with respect and an open mind. In some cases, managers and supervisors have to “unlearn” how they discuss and evaluate suggestions and ideas they get from their front-line employees. Again, it takes time, patience and practice to get the pump primed and the ideas flowing. It sounds easy, but it takes hard work to make an employee suggestion program become part of “the way we do things around here.”
With tailwind of the profit-sharing plan and the headwind of the missing employee suggestion program, the kaizen team members and management worked diligently through the “ups and downs” of the lean workshop. The team’s final presentations to management represented a breakthrough for both the team members and management in terms of expressing themselves (the PowerPoints were excellent), listening with an open mind and coming to agreements about the countermeasures and implementation plans.
And word traveled quickly around the shop about the quality of the final presentations and the effort put in by the team members. The simple but elegant solutions have been well received. The teams are still working on the implementation, but so far feedback from the floor and the management suite has been very positive.
There was a real growth on both the team members’ part and management’s part because of what they went through in the lean workout this summer. What they learned will show up in much more efficient processes that will prove to many on the floor that front-line employees have some valuable ideas and that management will give them a chance to implement them. My best guess is that an employee suggestion program is just around the corner and that this time it will catch on.
Mark S. Doman is a Pawley Professor in Lean Studies at Oakland University in the Human Resource Development Department and the Director of the Pawley Lean Institute. Prior to joining Oakland University, he had 25 years of business experience with Ford and AT&T, where he held various executive positions in operations, human resources and legal. He has led several major organizational change initiatives throughout his career that included corporate restructuring, Lean Workouts, kaizens, TQM and process re-engineering. He is the author of “A New Lean Paradigm in Higher Education: A Case Study.” Quality Assurance in Education, Vol. 19 No. 3, 2011 and “How Lean Ready Are You?” Target, Vol. 28 No. 2, 2012. His email address is doman@oakland.edu.