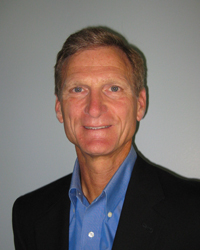
Winter term started a few weeks ago and a new, innovative lean course debuted at Oakland University in Rochester, MI. The new course, Lean Kaizen in Organizations, kicked off with 18 students including a combination of undergraduates from widely diverse majors and a number of nontraditional students.
Two of the nontraditional students are employees of a local manufacturing company — Fitzpatrick Manufacturing. The president of Fitzpatrick Manufacturing selected these participants to further their lean learning and also to be part of a kaizen team that will tackle a persistent problem with the company’s purchasing process.
This course marks the next step — a new level of partnership — in a growing relationship with Southeast Michigan manufacturing firms that started more than four years ago with the first lean undergraduate course at Oakland University, called Lean Principles and Practices in Organizations.
In that time, 15 manufacturing companies had participated in the lean course and opened their doors to Oakland University student teams to conduct Lean Assessments of their operations. It has been a tremendous learning experience for both the companies and the students. Many of the companies have incorporated the student teams’ findings and recommendations for improvement.
Now, we are taking this relationship to a new level of involvement and innovation. It really is an experiment to see if and how students and employees can study together in a classroom, learn about lean and then go out on the factory floor to work shoulder-to-shoulder on kaizen teams.
Can the students, many of whom have never heard of lean or been inside a factory prior to taking this course, understand and apply lean thinking and lean tools and techniques to work effectively on kaizen teams? Similar questions can be asked about the employees, many of whom are in a college classroom for the first time but are very familiar with the processes the teams are working on.
This new lean course provides students with a comprehensive “learn-do” experience that teaches them how successful lean Kaizens (continuous improvement) are conducted in business, government and education.
The six focus areas in the course are: Lean Philosophy, Lean Tools & Techniques, Teambuilding, Kaizen Methodology, Organization Change and Presentation & Facilitation.
This course provides students with the knowledge and skills related to lean theory, principles, concepts and tools, as well as key supporting HR policies and practices. The course includes several guest lecturers, site visits, case studies, group exercises and simulations. It also allows students the option of earning a Lean Green Belt Certificate.
Students will have the opportunity to be part of a kaizen team and will conduct a lean workout of a dysfunctional process. Students will quickly immerse themselves in learning about lean culture, lean tools and techniques, teambuilding and kaizen methodology, and then be assigned to a kaizen team. The kaizen team will work on a real-world process that is experiencing problems and not performing at an optimal level.
One of the three kaizen teams is sponsored by Fitzpatrick Manufacturing and includes the two Fitzpatrick Manufacturing employees who are taking the course plus three undergraduate students. We asked for volunteers and got some great students who are gung-ho to work on this kaizen team.
The president of Fitzpatrick Manufacturing and I worked closely together to select a challenging, yet doable process for the kaizen team to focus on in completing its lean workout during the term. We decided to focus on the raw materials and tools purchasing process which has been experiencing problems and is critical to meeting the company’s lead time, quality and cost requirements.
As part of the lean workout, the kaizen team will complete an A3 Report: define the problem(s), identify the ideal state, determine the current condition, analyze the causal relationships, design the target condition and formulate an implementation plan to achieve the target condition. The team members will then present their findings and recommendations to the team sponsors.
The team sponsors and I are hopeful that this new level of partnership will be a resounding success. The team sponsors have already starting working with their respective student teams. They were in class this week introducing themselves and describing process they have chosen for their teams to address and the various problems with it. Most importantly, they laid out their expectations to the teams and challenged them to exceed them.
The students are excited by the challenges, the team sponsors are all in and I’m excited to see how well it works. I’ll let you know in May when the class is over and all the results are in.
Mark S. Doman is a Pawley Professor in Lean Studies at Oakland University in the Human Resource Development Department and the Director of the Pawley Lean Institute. Prior to joining Oakland University, he had 25 years of business experience with Ford and AT&T, where he held various executive positions in operations, human resources and legal. He has led several major organizational change initiatives throughout his career that included corporate restructuring, Lean Workouts, kaizens, TQM and process re-engineering. He is the author of “A New Lean Paradigm in Higher Education: A Case Study.” Quality Assurance in Education, Vol. 19 No. 3, 2011 and “How Lean Ready Are You?” Target, Vol. 28 No. 2, 2012. His email address is doman@oakland.edu.