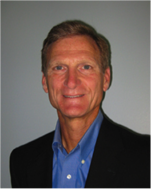
In my experience, there are several roads to a successful root cause analysis of a business problem.
The road, though, that gets all of the ink in lean books and articles is the 5-Why Analysis. And well it should. It confronts head-on our tendency to grab the first solution that looks good and run with it.
The 5-Why Analysis is a disciplined approach to problem solving, and it casts a wide net (think 4M and 1E and fishbone diagrams). Its goal is not to stop until you get to the root cause — the cause that will prevent the problem from recurring. 5-Why Analysis goes against our impulse to “solve” the problem fast and get on to the next one. This road requires patient fact-finding and analysis, which often collides with our penchant for flashy firefighting. And that’s good, but it often stumps lean beginners or leads them on a wild goose chase.
There is another road to root cause analysis that is better suited to lean beginners and will lead to the real root cause in the majority of problems. It is a superhighway to uncovering what is causing your process problems, and it starts with three easy questions. It is the right road for the lean beginner to start on.
The first and most fundamental road to root cause analysis has easy-to-understand questions and tough-to-swallow answers. It revolves around standards or lack thereof. The questions to ask are straightforward. There are three of them:
1. Are there standards? Are they simple, clear and visual? Do they depict a clear image of the desired condition? Do they make abnormalities immediately obvious? Are they prominent in the workplace or hidden in a binder on some dusty shelf? Do they look similar to this (see photo below) in the workplace?
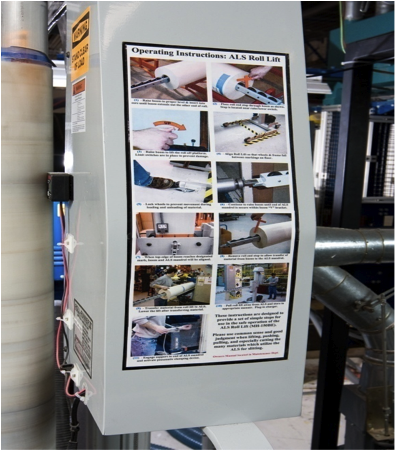
If the answer is “no” to any of these questions, then you don’t have effective standards!
2. Do employees know the standards? Do the employees doing the work know what the standards are? Do the employees who supervise the employees doing the work know what the standards are? Does the management team know what the standards are? Is there a continuous training program with standardized work charts (see below) for employees to learn all the standardized work they may perform in their work group?
If the answer is “no” to any of these questions, then you don’t have effective standards!
3. Do employees follow the standards? Do the employees doing the work follow the standards on a consistent basis? Do the supervisors monitor and work with employees to ensure that the standards are followed on a consistent basis? Does the management team monitor its supervisors and require adherence to the standards?
If the answer is “no” to any of these questions, then you don’t have effective standards!
What you do have, though, is a big, flashing neon arrow pointing to the root cause(s) of your process problem(s).
Now, management should look in the mirror and start asking, “Why?” Managers and kaizen teams want to find exotic root causes so they look insightful and brilliant, but the answers are generally staring them right in the face.
As Taiichi Ohno said (probably many, many times in his career): “Without standards, there is no kaizen.”
Standardization is the least sexy part of lean (as I’ve written before in an earlier Target Online article), but it is the most fundamental part of lean, and the lack of effective standardization leads, more often than not, to the root cause of most manufacturing problems.
Mark S. Doman is a Pawley Professor in Lean Studies at Oakland University in the newly formed Department of Organizational Leadership. Prior to joining Oakland University, he had 25 years of business experience with Ford and AT&T, where he held various executive positions in operations, human resources and legal. He has led several major organizational change initiatives throughout his career that included corporate restructuring, Lean Workouts, TQM and process re-engineering. He is the author of A New Lean Paradigm in Higher Education: A Case Study. Quality Assurance in Education, Vol. 19 No. 3, 2011 and How Lean Ready Are You? Target, Vol. 28 No. 2, 2012. His email address is doman@oakland.edu.