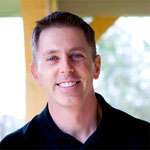
Over a year ago, I toured a facility that had undergone what the executives called “a lean transformation.” The organization had improved productivity numbers after introducing a series of kaizen events. Downtime and changeover time had been reduced, and product flow was considered to be optimum.
During the tour, I walked down the aisle of one of their large presses and found a significant oil leak pooling on the floor. When I asked an employee what was causing the leak, he responded that it had been around for years. When I entered the product testing area, it was difficult to assess where one product and its testing documents ended and another began. Tabletops were littered with documents. In the shipping department, water seeped in under several shipping doors, gathering in slippery pools on the floor, the result of overhead doors being either broken or dismantled.
If these were the signs of a lean transformation, then what this organization needed was a lean apocalypse.
In speaking with the lean coordinator and general manager for the site, he admitted that although the kaizen events had improved process efficiency, it had not shifted culture necessary to support continuous improvement.
I’ve heard similar comments from other business owners and executives, and I’ve found (not surprisingly) that the use of kaizen events appears to be on the decline. From my analysis, there appear to be a few simple reasons for this trend:
- The misperception that a kaizen event is the start and end of a continuous improvement journey
- Failure to remain agile with the ongoing management of changes associated with the kaizen event
- Loss of focus on the key objectives that precipitated the kaizen event in the first place
- The cultural perceptions that results achieved during a kaizen event are not sustainable
- A desire to handle kaizen events 100 percent in-house rather than engage outside resources for support
Notice a trend here? It’s not the approach to how the Kaizen is introduced or handled; it’s how the results are sustained. It doesn’t matter what type of initiative you undertake, success resides in the follow-up. Heck, we can all become engaged for a day or so, but it takes longer to formulate new habits.
If you are embarking on, or have embarked upon, a lean journey incorporating kaizen events and you want to achieve a cultural shift that supports continuous improvement, then consider including the following to ensure sustained momentum:
- Reconvene the kaizen team at 30, 60 and 90 days following the events to review outstanding actions and new ideas or challenges that have arisen during the early stages of change.
- Ensure that front-line managers affected by or included in the Kaizen are coached for a period of three months following the event to ensure they fully embrace the new ways of doing business, and to support their efforts to continue to engage employees involved or affected by the change.
- Introduce simple, yet effective, employee suggestion programs to capture new employee ideas that begin to surface. Most importantly, empower an employee board to review and act upon ideas that support improvement, ensuring that every idea submitted receives a quantitative or qualitative response within 30 days.
Capturing the value that a kaizen event can produce is critical to building momentum for future improvement. By introducing a robust means of follow-up, you can improve the speed by which change is integrated, and ensure an effective cultural shift is both supported and nurtured.
Shawn Casemore is the president and founder of Casemore & Company in Ontario, Canada.